一般に、多層基板と二層基板の製造工程と比較して、それぞれインナーラインとラミネートの2つの工程が増えます。
詳細: 二層プレートの製造プロセスでは、切断が完了した後、銅、ラインに穴あけが行われます。多層基板の製造プロセスでは、材料の開口が完了した後、直接穴あけは行われませんが、まず内側のラインとラミネートを通過し、次に穴あけ作業場に入って穴あけする必要があります。銅線と線路に。
つまり、開口と穴あけの間に「インナーライン」と「ラミネート」という2つの工程が追加されます。以上が多層基板と二層基板の製造の違いです。
次に、インナーラインとラミネートの2つの工程が何をしているのかを見てみましょう。
内側のライン
フィルムの圧縮、露光、現像など、二層版の製造における「ライン」プロセス (忘れた場合は戻って確認できます)。
ここでの「内部回路」はそれほど単純ではありません。内部ラミネートフィルム、内部露光、内部現像に加えて、内部前処理、内部エッチング、内部膜除去、内部 AOI も含まれます。
2層板の製造工程では、銅蒸着後の基板を生産ラインを使わずに直接プレスフィルムに完成させるため、追加のプリプレス処理が不要です。そして、ここの銅箔板は、切断工場から来たばかりなので、板の表面には不純物が付いています。
内側のラミネートフィルムの前に、化学反応を利用した処理と洗浄を進める必要があります。最初に油、水、浄水の除去、2回のマイクロエッチング(表面のゴミの除去)、次に水、そして酸洗(後)洗浄すると表面が酸化するので酸洗いが必要)、その後水をかけ、乾燥させてから内側のラミネートフィルムに入れます。
処理前のインナーラミネートフィルム
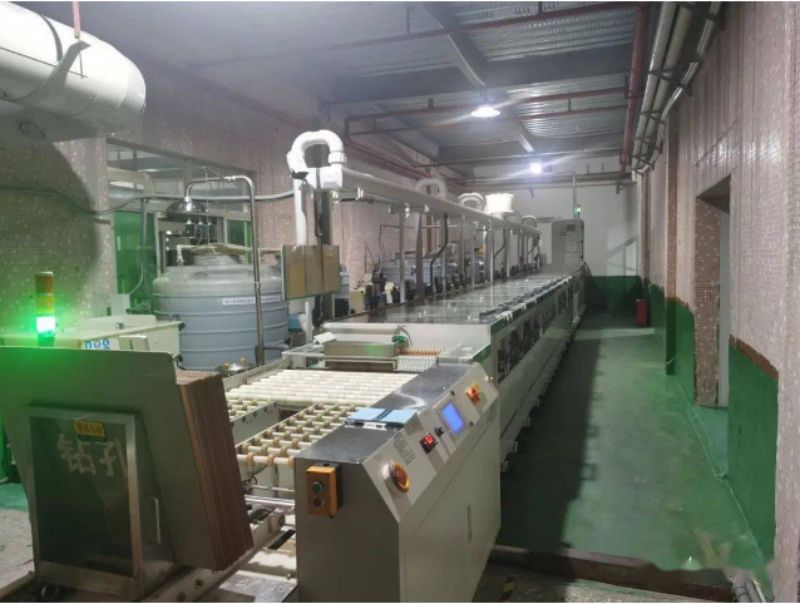
基板をプレスした後、穴が開けられていないため、非常に平坦に見えます。
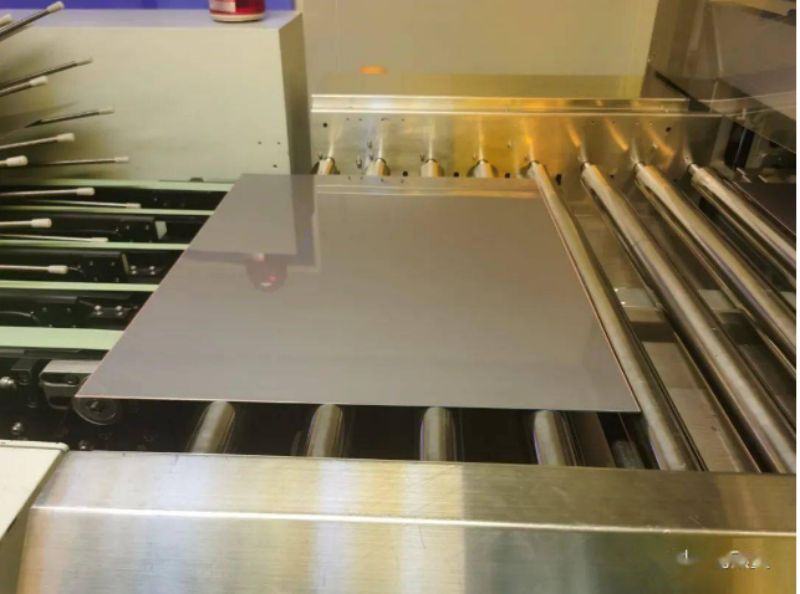
フィルムのプレス、露光、現像、これらのリンクの具体的な事項は、二層版の作成の記事で紹介されているので、ここでは繰り返しません。
外層はポジ処理、内層はネガ処理のため、現像が完了すると真鍮の一部が露出します。したがって、外層現像完了後、露出したライン銅は残す必要がある部分となり、内層現像後に露出した銅はエッチング除去する必要がある部分となります。
内側のエッチング工程と外側のエッチング工程も異なり、内側のエッチングはアルカリ性の処理で、エッチングの際にはドライフィルムが残っており、ドライフィルムのない部分(露出した銅)が先にエッチングされ、その後、金型が取り外されます。
外層のエッチングは最初に除去され、次にエッチングされ、ラインは液体錫で部分的に保護されます。
内側の膜エッチングライン、左側がエッチング、右側が膜の除去を担当します。
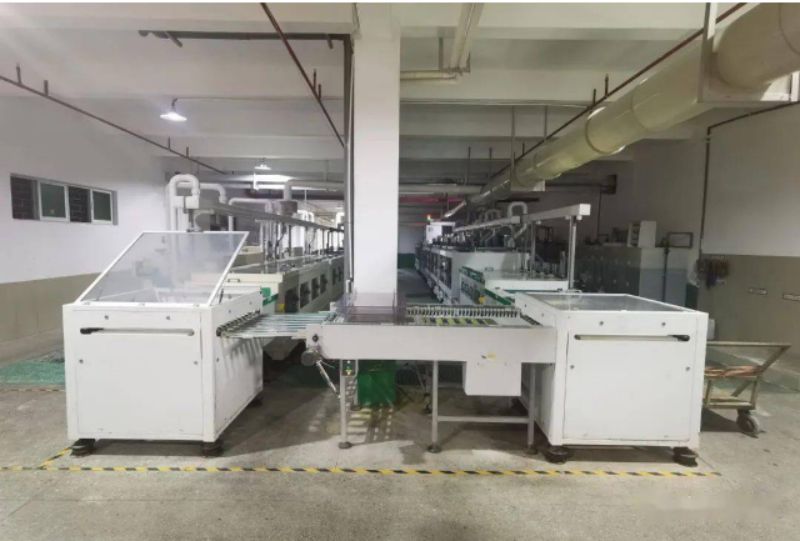
回路基板をエッチングした後、余分な銅はエッチングで除去されており、ドライフィルムの残りの部分は除去されていません。
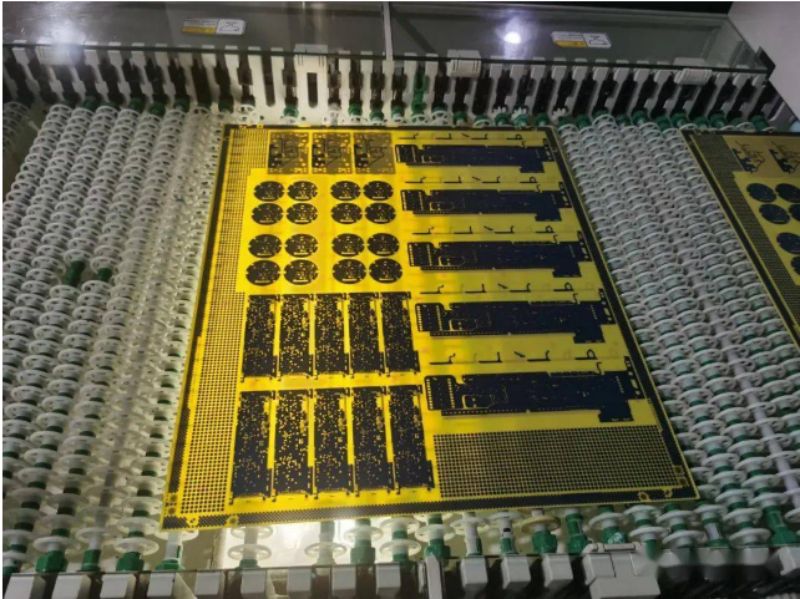
剥離後の基板。
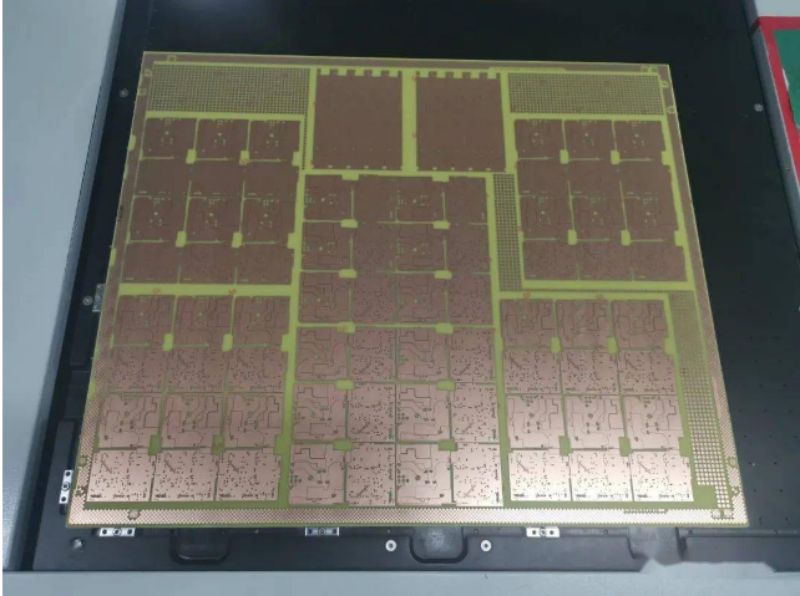
フィルムの内層が完了し、ラインの内層が完全に完了したら、この時点でAOI光学検出を行い、問題がないことを判断して、ラミネートプロセスを実行できます。
ラミネート:
作ったばかりの基板をインナーコアボードと呼びます。4 層の基板の場合は 1 つのインナーコアボードがあり、6 層の基板の場合は 2 つのインナーコアボードがあります。
このプロセスの主な目的は、内側のコア プレートと外側の層を接着して全体を形成することです。PPと呼ばれる接着材料を担当し、中国では半硬化シートと呼ばれ、主な組成は樹脂とガラス繊維であり、内側のコアボードと外側の銅箔絶縁の目的も果たします。
多層基板の品質を確保するため、嘉里荘市のPPサプライヤーは依然としてSouth Asia Electronicsです。
一般にラミネート工程は、ブローニング、プレスタッキング、プラテン、プレスの順に 4 つのステップに分かれます。次に、各工程の詳細を個別に見ていきますが、皮膜除去が完了した内芯板は、まず焼き色が付けられます。褐色基板は、PPとの接着を容易にするために、茶色のメタライズド基板の表面に凹凸のある褐色フィルムの層を追加します。
自転車のタイヤを修理するときと同じ原理で、壊れた箇所をやすりで削って接着剤の密着性を高めます。
褐変プロセスは化学反応プロセスでもあり、酸洗い、アルカリ洗浄、マルチチャンネル洗浄、乾燥、冷却などのプロセスを経ます。
プレラップ
粉塵のない作業場で行われるプレスタッキング工程では、コアプレートとPPを一緒に積み重ねます。コアプレートの両面にPPを配置します。プレス後の端部の空洞を防ぐため、PPの長さおよび幅はコアプレートより2mm大きくなります。
ラフト:
列プレートの主な目的は、後続の外側のラインを準備するために、PP 層の上に銅箔の層を追加することです。さらに最外層に鋼板とクラフト紙を加えて積層します。
最初のいくつかのステップは、最終ラミネートの準備です。
ラミネートする前に、反りを防ぐために、厚さ約 12 mm のスチール製のカバープレートが存在します。
ラミネート加工には、ホットプレスとコールドプレスの 2 つの工程が含まれます。これは、高品質の回路基板を製造するために、真空、温度、圧力、時間などの要因を考慮する非常に重要なリンクであり、これらの要因が相互に連携して作用します。
たとえば、一定時間内で、どのくらいの温度、どのくらいの圧力、必要な時間を正確に調整する必要があります。
このプロセスの終了後、PP と内側のコアプレートおよび外側の銅箔は互いに密接に接続されます。
プレスから出た後は自動解体が行われ、鋼板が取り外され、研削後再び小隊室へ送られます。図 11 に示すように、機械は鋼板を取り外しています。
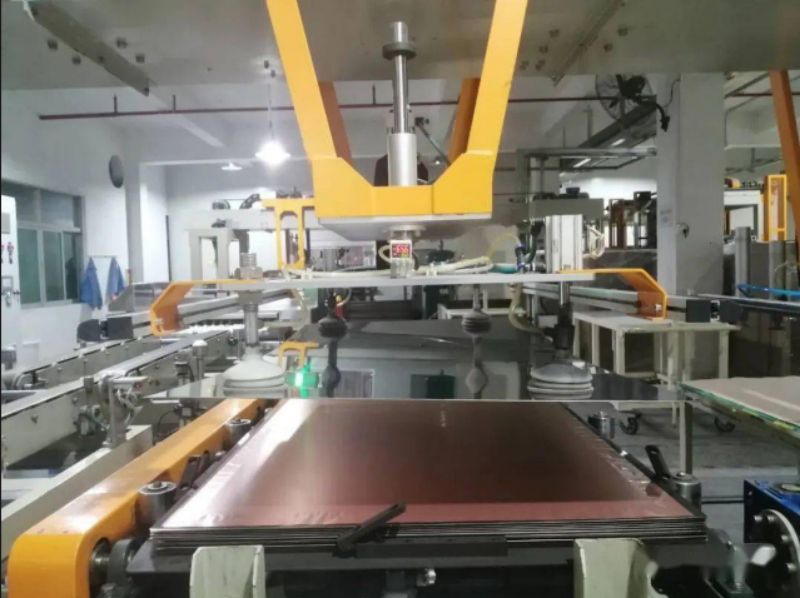
積層された多層回路基板は元の穴あけ作業場に戻されて穴あけ加工が行われ、残りのプロセスは二層基板の製造プロセスと同じです。